Dr Ray Wan
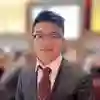
About Dr Ray Wan
Dr. Wan is a Lecturer in the School of Mechanical Engineering at the University of Hull. He is also a Chartered Engineer (CEng) and a member of the Institution of Mechanical Engineers (IMechE). He holds a professional membership at the Institute of Materials, Minerals and Mining (IOM3). He is also a Fellow of the Higher Education Academy (FHEA).
Dr. Wan obtained his PhD degree from the University of Edinburgh in 2020 on computational modelling of fibre-reinforced composite materials. Then he worked on the prototype of green manufacturing of carbon fibre-reinforced composites for 3D printing. Since 2021, he has worked as a research fellow at the Queen's University Belfast with local industrial collaborators from the aerospace (Collins Aerospace and Spirit Aerosystems, Belfast) and maritime (Artemis Technologies Ltd) industries, addressing the challenges in the application of AI in the composite structural design. From 2023, he moved to the world-leading Bristol Composites Institute (BCI) as a research associate and worked as a core team member at the unique Rolls-Royce Composites University Technology Centre (UTC). He has been working on the multiscale modelling and digital twinning of engineering structures for sustainable energy. He then moved to a visiting position at the University of Bristol and joined the University of Hull as a lecturer in 2024.
- --------- Publishing Opportunities -----------------
Ray Wan is also the guest editor for a Special Issue (SI) of Applied Sciences (IF2.5) on the topic of “Micromechanical Analysis of 3D Printed Fiber-Reinforced Composites” (https://www.mdpi.com/journal/applsci/special_issues/MF9085I1X7). This SI focuses on leveraging micromechanical analysis to address the emerging manufacturing induced challenges. By examining fibre–matrix interactions, failure mechanisms, and the effects of 3D printing parameters at the microscale, this SI aims to bridge the gap between material design and performance prediction. We invite contributions on topics including, but not limited to, multiscale modelling, experimental characterisation, process–structure–property relationships, and the development of innovative methods to enhance the mechanical performance of 3D printed fibre-reinforced composites.